
NOISE ASSESSMENT AT WORK - WORKPLACE NOISE SURVEYS
Noise assessments for all workplaces nationwide, measuring employee noise exposure levels to help companies comply with the HSE’s Noise Regs.
All UK covered ● Experienced noise assessor ● Daily average noise exposures ● Assessment of hearing protection ● Wearable and hand-held noise monitoring ● Institute of Acoustics certified ● NEBOSH Diploma ● 30 years of experience ● Noise assessments to meet the HSE’s Noise Regs.
“Thank you again for our report, it’s great. Really understandable and easy to follow”
Compliance Manager, Northampton, 2025
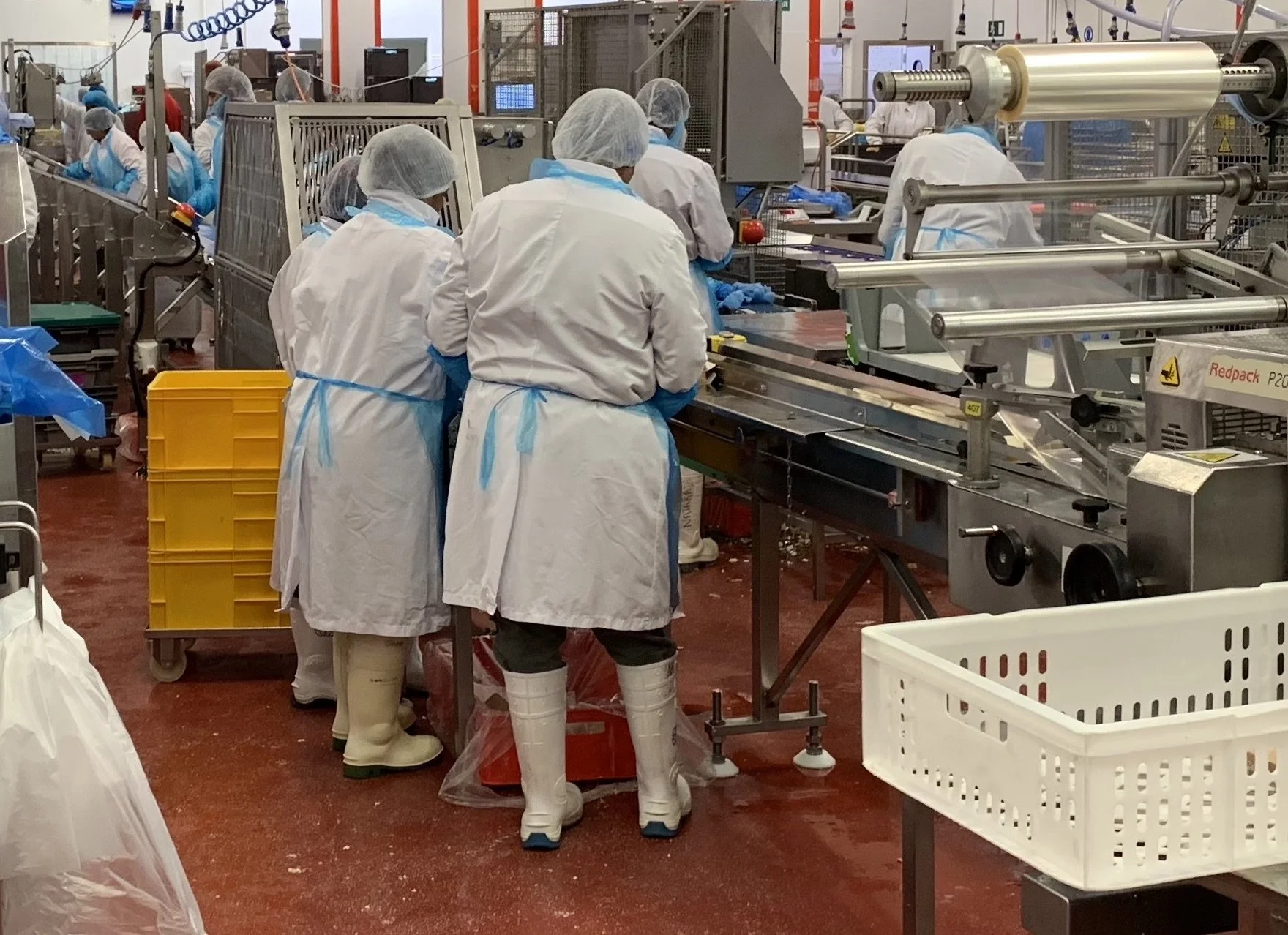
Noise assessments for any workplace, anywhere in the UK
Over 600 noise assessment clients, ranging from companies with three people to those with over 20,000, plus organisations like the NHS.
food industry ● joinery ● engineering ● packaging ● pharmaceuticals ● groundskeeping ● vehicle maintenance ● shipping
motor industry ● foundries ● plastics ● hospitality ● recycling ● local councils ● retail ● windows and doors
“This noise report is fantastic, we will certainly be using you again in the future, a very knowledgable chap as well”
Training and SHE officer, Lincolnshire, May 2025
Noise assessment contents
All my noise assessments identify employee noise exposures (both averages and peaks) and assess hearing protection suitability, both current and potential alternatives. They also look at sources of noise and potential controls that could be used. The noise assessment looks at training and health surveillance needs.
Simple on the day
Point me at the area you want the noise survey to cover and I will assess the dB(A) and peak dB(C) levels, using whichever type of noise meter best suits the jobs taking place. Noise measurements are made for as long as is needed to get a good result. For jobs which are not running, sample measurements can be done.
The noise assessment report
My noise assessment report gives a summary of the key findings followed by specific results details as simple headlines, and detailed recommendations for those who want to dive into it more deeply. I go through hearing protection, identify who needs noise training and who may need the ongoing health surveillance.
“I would just like to thank you for your time on site, and the professional manner in which the noise assessment was conducted. Your report also reflects this, I've found it very easy to read and from which to produce an action plan.” - MD of an engineering site, Newcastle
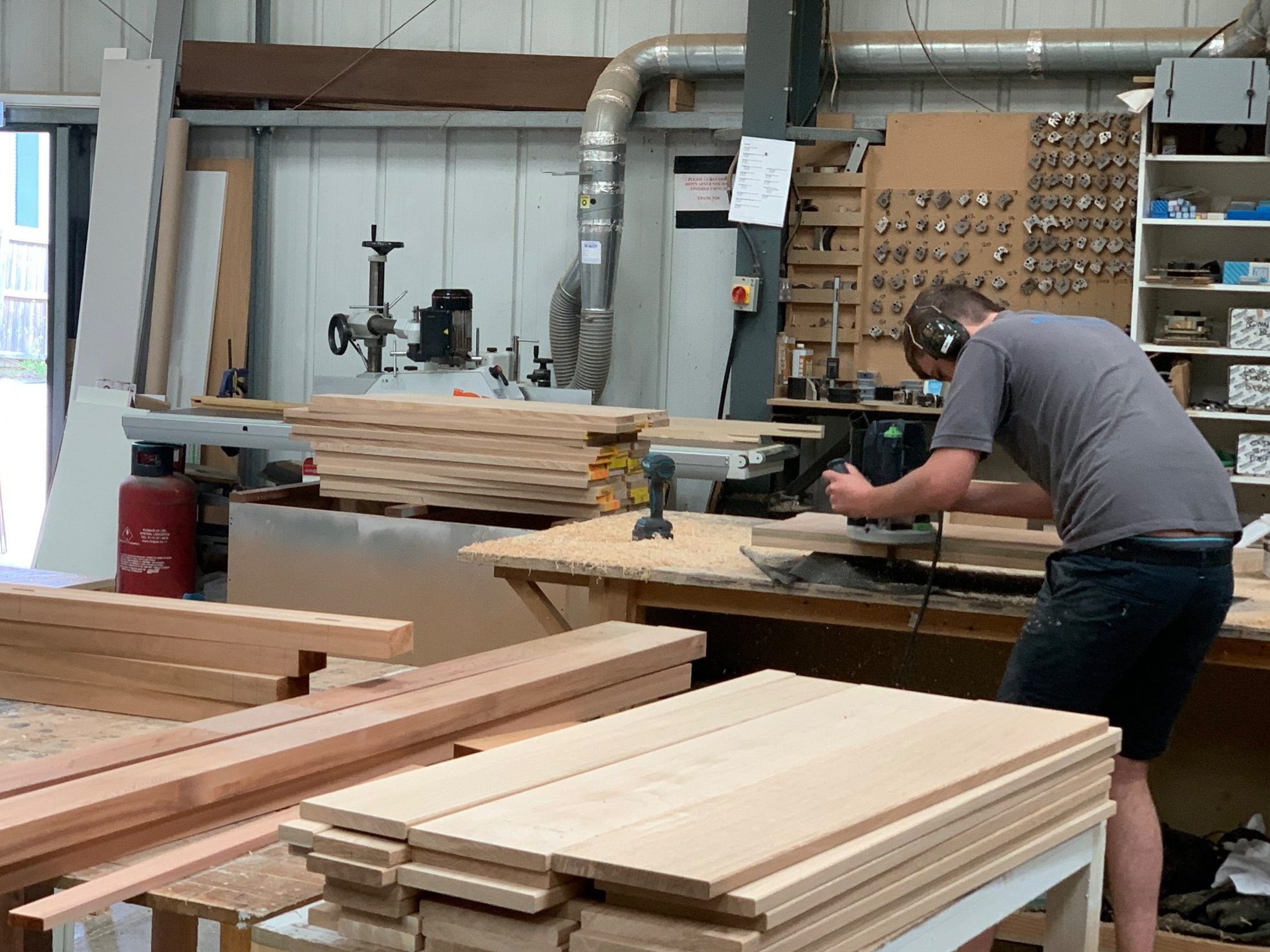
What is an occupational noise assessment?
A noise assessment or noise survey is a measurement of the noise risks which employees are exposed to at work, it is a measurement looking at daily noise exposures and what needs to be done to control the risk.
As well as the noise levels, a noise assessment looks at hearing protection to make sure it is suitable for the noise risks present, identifies other possible noise reduction measures, looks at what signage is needed, and flags who needs other mandatory actions such as noise safety training and health surveillance (the regular hearing testing).
My noise assessments and the reports give clear plain-English advice on exactly what the noise risks are in the workplace and outline what employers need to do to manage the noise risk for employees. The noise assessment covers the noise measurements needed to keep the HSE happy and tells you exactly what ongoing measures are needed for Noise Regs compliance, in an easy to follow way.
What is a noise assessment - a quick guide to what a noise assessment contains for employers.
“Morning Adam, once again thank you for an excellent noise assessment report for our Bolton site.”
Production Manager for chain of packaging sites, September 2024
Workplace noise assessment specialist, or to be less charitable, a proper noise-nerd for hire
Who needs a noise assessment?
Basically, any place of employment (or where volunteers work) where noise levels may be over 80 dB(A). As a guide, do you need to raise your voice to have a conversation? If so a noise assessment or noise survey is needed to measure the noise levels and identify if there is an issue.
How long does a noise assessment take?
It depends on the production cycles and I will be there as long as is needed to get all the noise risk data. I have 15 noise meters so the noise assessment can cover a wide area quite quickly - effectively in every hour I can gather 15 hours’ worth of noise data.
Am I better than the big boys?
Yes indeed, very much so. Put it this way, if my noise assessment is found lacking then I have no faceless corporate edifice to hide behind, it will be me the HSE jump on and send to share a small cell with Big Dave and his wandering hairy hands. I have direct accountability for each noise assessment and for the ongoing success of my business.
Superb value noise assessments
As I am just me there is no corporate office filled with overly expensive chairs clients are paying for, no hoards of shiny-suited sales reps, nothing to add extra fixed costs. That means I do noise assessments which are extremely high quality but at a very competitive cost as I don’t have the overheads of the corporates.
Noise assessments for HSE Noise Regs.
My noise assessments cover the noise exposure levels in the workplace, assessment of the hearing protection, advice on some noise reduction measures, and identifying any training or hearing testing (health surveillance) needs. If you’ve had a horned devil from HSE in, my noise assessment is what you need.
My competence for noise assessment
Institute of Acoustics certified, NEBOSH Diploma, and over 30 years of experience in workplace noise assessment.
Also a member of the British Society of Audiology so have superb understanding of noise safety and the health impacts of noise.
“Thank you for the noise assessment report, very informative and very well put together”
Engineering site’s Managing Director, Wolverhampton, on a noise assessment for them in 2024.
Noise assessment quote
How the noise assessment process works
The noise assessment itself - on the day
I will rock up, ask a few questions about things like training history, hearing protection policies, shift patterns, etc. then get on with measuring the noise levels.
That can include putting some wearable meters on the shoulders of some people, using long-term meters in certain positions, and always wandering around with a hand-held meter to get detailed noise measurements for various tasks.
People should just carry on and work as normal, there is nothing special needed from the client on the day. If they have stereos on then it is OK to leave them on, the more ‘normal’ the day of the noise assessment is the better.
The one exception is non-running equipment where to get a measurement someone will need to fire it up for a quick measurement but that needn’t be a long process.
Places like joinery or engineering workshops can be a little different as there is often no set working routine here, with different jobs each day. In places like this I need someone to quickly operate each tool so I can get a reading from it.
The noise assessment report
You’ll then get a noise assessment report which I have honed over the years and am rather proud of to be honest. It will tell you in non-jargon plain-English what the noise issues are, if any, and what I recommend is done as any follow-up actions.
If you have had the HSE on your back this will be exactly the information needed to help there so covers off all the essentials like assessing the risk levels, confirming if the PPE is suitable for the noise, identifying precisely any training or hearing testing needs, etc.
“Thank you so much for all your help. I'd also just like to say that the report is extremely helpful from the point of view of someone who is not a noise expert so thank you for that!” - Workshop Manager, London, May 2025
Want to know more about industrial noise assessments or workplace noise surveys?
How often should you repeat a noise assessment?
Noise assessment isn’t a one-shot process and you do need to repeat them every so often, but that doesn’t always mean getting someone like me in every time. As much as my bank balance would thank you, you can do reviews in-house and then get a new assessment done from scratch less frequently.
For the in-house review, have a look around and has anything changed? New equipment, machines moved around, shift lengths changed, etc.? If the answer is no then you are done. Document that you did it.
The less frequent repeat is something I would advise roughly every three years which will catch things like small unnoticed changes to a motor here and there, etc. This is my recommendation and no matter what other consultants tell you, there is no law about when you must redo the whole thing from scratch.
8 hour exposure limits and the time needed to do a noise assessment
The limits in the Noise Regs relate to eight hour daily average exposures but that doesn’t mean a noise assessment has to be over eight hours. If someone works on a machine which has a cycle of anything from a minute to half an hour, once you have measured the noise for a few cycles you will have a level for it. From that point on it doesn’t matter how long you measure for, the result is exactly the same.
What also matters is how many noise meters are being used. I have 15 so in three hours of assessment I am doing the equivalent of 45 hours of measuring. The time on site is not related to the number or accuracy of measurements. What I don’t do is pad out the time to make the invoice bigger.
Read more on dealing with eight hour averages and how long a noise assessment should take
What are the obligations for employers for getting a noise assessment done and then managing noise risks?
If there is reason to think noise levels may be approaching 80 dB(A), then they need to arrange a noise assessment to confirm the actual noise levels present.
If the noise assessment gives levels of 80 to 84 dB(A) then all employees need to have noise safety training and hearing protection has to be available, but employees can choose whether to wear it or not.
If the noise assessment shows levels are 85 dB(A) or over then everything else applies, so the training element along with mandatory hearing protection and mandatory hearing testing. Employers also have to reduce noise levels as much as is reasonable or possible to do so.
Read more on the legal requirements for managing noise at work
Noise assessment vs noise risk assessment - what’s the difference?
A noise assessment is what an employer needs to do if there is reason to think noise levels may be averaging over 80 dB(A) in all or part of the workplace. That is an average for the shift by the way, not individual instances.
The noise assessment works out what the daily noise exposure is likely to be for people, and as all hearing protection is different it assesses if the hearing protection is OK for the specific noise risk. It also looks at who needs noise training and things like hearing testing.
A noise risk assessment is a very simple document referencing that, and also things like the in-house policies for issuing and controlling PPE, who manages the hearing testing programme, etc.
Other nuggets of noise safety info.
USING NORMAL HEADPHONES / EAR BUDS IN A HIGH NOISE AREA: This is an increasingly common issue, but no, it can’t be done. HR or GP’s do not have the power to over-rule this.
Read more on using music headphones in a high noise area or exemptions from use of hearing protection.
HANDHELD VS WEARABLE NOISE METERS: A noise assessment may include noise measurements made with hand-held, static or wearable noise meters, what is important is the right meter for the job.
Read more on types of noise meter used in a noise assessment.
NOISE SAFETY TRAINING: Once you have got the noise assessment, if levels are over 80 dB(A) then there is a requirement to train all staff who may work in that area. The HSE are very specific on what that training must contain.
Read more on noise safety training requirements
DB(A) and DB(C): You need not one but two types of noise measurement in the noise assessment - dB(A) and dB(C).
Read more on dB(A) vs dB(C)
“Thank you for all the noise safety information provided in the noise assessment and arranging it for us. Would just like to say I really appreciate all the knowledge you have shared with me as the guidance alongside the results really helped. This is a pretty new process for our site due to the recent introduction of new machinery and I have found the noise side of it very interesting. I will be sure to highly recommend your company to our sister site in England”. - H&S Manager, Irvine, Scotland
Noise assessments can even sometimes save you money
With a fair wind behind you and some luck, as well as keeping the HSE and your insurer happy, just occasionally a noise assessment can save a considerable chunk of money for clients. Recent cases have included:
A noise assessment for a new client who was also planning on getting over 200 hearing tests done every year as it sounded noisy in their factory. The noise assessment showed the averages to be well below the 85 dB(A) limit though so hearing tests were not needed, a saving of around £5k per year.
A client had used a phone app to look at their noise, decided it was high, and several years ago started getting all 380 staff covered with hearing testing at a cost of nearly £10k a year. They asked for a proper noise assessment and it confirmed that of the 380 staff, they actually only needed to get hearing tests done for 14 of them. So from £10k to about £500, each year.
A small client had done hearing testing for years as they thought it was noisy but had never measured the noise. My noise assessment confirmed it was not needed so that ongoing cost could be dropped as there was no risk.
Another small company had been told by their insurer that they thought hearing tests should be done as ‘it sounds noisy’. My noise assessment showed it was nowhere near the limits and hearing testing was not needed, again, an ongoing saving every year.