
Noise assessment at work - workplace noise surveys
Noise assessments for all workplaces nationwide, measuring employee noise exposure levels to help companies comply with the HSE’s Noise Regs.
All UK covered ● Experienced noise assessor ● Daily average noise exposures ● Assessment of hearing protection ● Wearable and hand-held noise monitoring ● Institute of Acoustics certified ● NEBOSH Diploma ● 30 years of experience ● Noise assessments to meet the HSE’s Noise Regs.
“Thank you again for our report, it’s great. Really understandable and easy to follow”
Compliance Manager, Northampton, 2025
What is an occupational noise assessment?
A noise assessment or noise survey is a measurement of the noise risks which employees are exposed to at work, it is a measurement looking at daily noise exposures and what needs to be done to control the risk.
As well as the noise levels, a noise assessment looks at hearing protection to make sure it is suitable for the noise risks present, identifies other possible noise reduction measures, looks at what signage is needed, and flags who needs other mandatory actions such as noise safety training and health surveillance (the regular hearing testing).
My noise assessments and the reports give clear plain-English advice on exactly what the noise risks are in the workplace and outline what employers need to do to manage the noise risk for employees. The noise assessment covers the noise measurements needed to keep the HSE happy and tells you exactly what ongoing measures are needed for Noise Regs compliance, in an easy to follow way.
What is a noise assessment - a quick guide to what a noise assessment contains for employers.
“Morning Adam, once again thank you for an excellent noise assessment report for our Bolton site.”
Production Manager for chain of packaging sites, September 2024
Workplace noise assessment specialist, any industry, anywhere in England, Scotland or Wales
I focus on just one thing, noise assessments, done well.
Clearly a noise expert
The onsite noise assessment itself
Using high quality wearable and Type 1 hand-held noise meters and dosimeters, I can undertake noise assessments in workplaces with anything from two to 2000 employees, anywhere in the UK. With up to 15 noise meters in use, quite large areas can be covered quickly and effectively.
Employer’s noise survey report
My noise assessment reports are written to give clear advice for the employer with straight-forward ‘these are your noise exposure levels and this is what you need to do next’ advice. The additional technical detail is also then included for those who wish to dive deeper.
Extensive noise safety experience
Whether this is good or a bit tragic I am unsure, but I now have over three decades of experience in noise assessments for the Noise Regs, including 20 years as a specialist noise assessor. There cannot be an industry left now in which I haven’t got some relevant experience to get the assessment right.
Noise assessments for HSE Noise Regs.
My noise assessments cover the noise exposure levels in the workplace, assessment of the hearing protection, advice on some noise reduction measures, and identifying any training or hearing testing (health surveillance) needs. If you’ve had the HSE in, this assessment is what you need.
“Thank you for the noise assessment report, very informative and very well put together”
Engineering site’s Managing Director, Wolverhampton, on a noise assessment for them in 2024.
Noise assessment competence
Institute of Acoustics certified, NEBOSH Diploma, and over 30 years of experience in workplace noise assessment. Also a member of the British Society of Audiology and done thousands of workplace hearing tests. I have a thorough knowledge of the practicalities of noise assessment and the associated health issues.
Simple on the day
Point me at the area you want the noise survey to cover and I will assess the dB(A) and peak dB(C) levels, using whichever type of noise meter best suits the jobs taking place. Noise measurements are made for as long as is needed to get a good result. For jobs which are not running, sample measurements can be done.
The noise assessment report
My noise assessment report gives a summary of the key findings followed by specific results details as simple headlines, and detailed recommendations for those who want to dive into it more deeply. I go through hearing protection, identify who needs noise training and who may need the ongoing health surveillance.
“I would just like to thank you for your time on site, and the professional manner in which the noise assessment was conducted. Your report also reflects this, I've found it very easy to read and from which to produce an action plan.” - MD of an engineering site, Newcastle
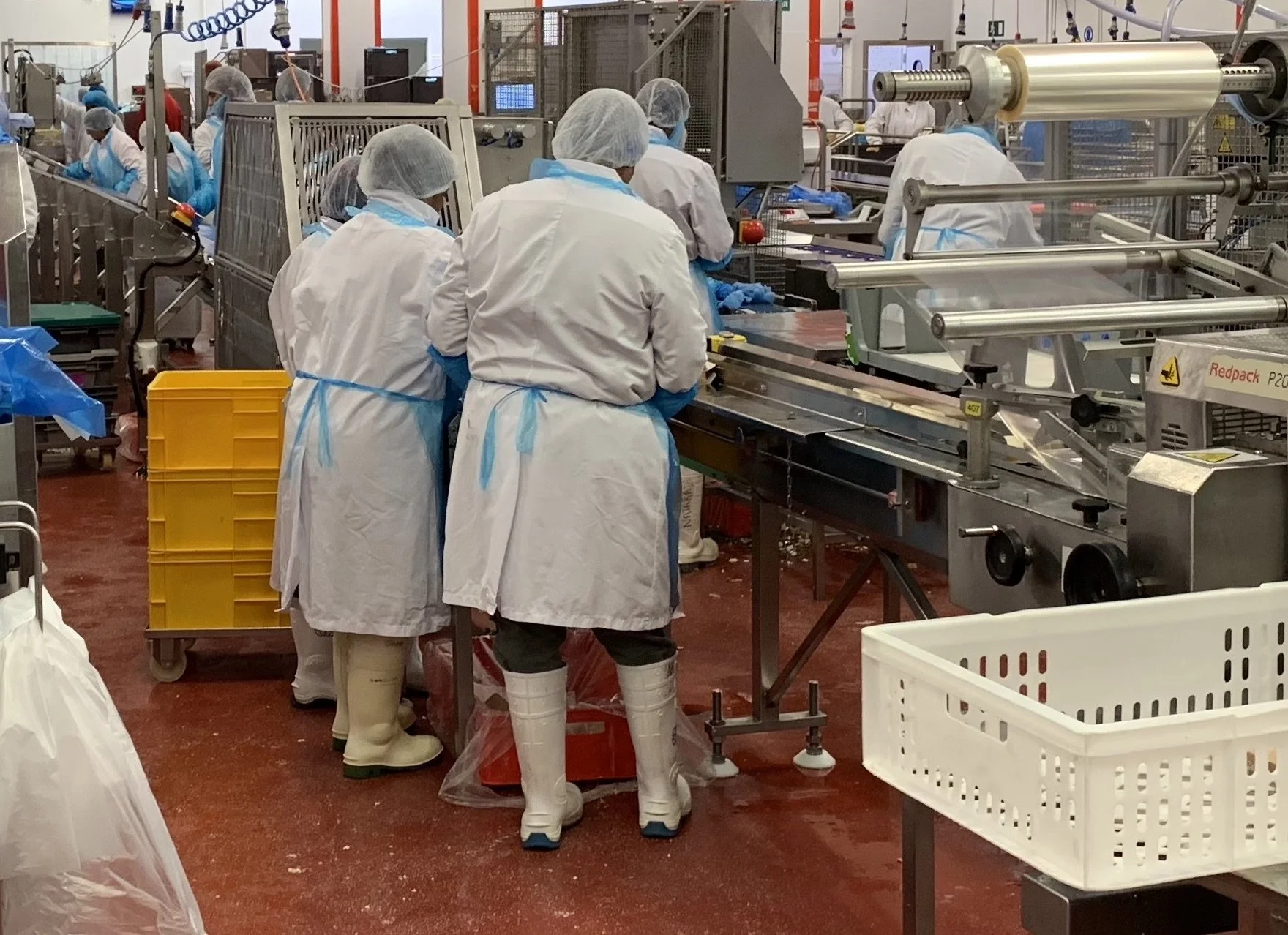
I work anywhere in England, Scotland and Wales and in any type of industry.
I’ve done noise assessments for satellite production, many food factories, the army, airports, packaging factories, joinery or engineering workshops, ship building, NHS hospitals, vehicle repair workshops, ships at sea, recycling centres, local Councils, schools and colleges, maintenance departments for shopping centres, window and door manufacturing and many more.
With over 600 clients now, they range from companies with three people while the largest employs over 45,000, plus organisations like the NHS.
My noise assessments give clear, simple advice for employers on who has a noise risk in their job and what the employer needs to do next for noise safety. Having sat on your side of the desk for many years I write my noise assessment reports in a non-jargon-laden way so employers get straight-forward information rather than just handing over a massive table of rather baffling numbers and dense noise-nerd terminology.
I have done noise assessments from RAF bases in Scotland to ice cream factories in Cornwall, paper making factories in Kent to timber mills in Pembrokeshire. There can’t be an industrial estate left in the West Midlands or North West where I haven’t waved a noise meter around with reckless abandon at some point.
Whatever your industry, wherever you are in the UK, I can provide a high quality workplace noise assessment for you.
Noise assessment quote
How the noise assessment process works
The noise assessment itself - on the day
I will rock up, ask a few questions about things like training history, hearing protection policies, shift patterns, etc. then get on with measuring the noise levels. I will use a variety of meters such as hand-held, location or wearable ones placed on people’s shoulders, whichever gets the best result. On the day it is very simple and there is nothing a client needs to do to prepare for it, just work as normal.
The noise assessment report
Afterwards I will send you a noise assessment report which includes:
What your noise levels are and how that compares to the legal noise limits so you can easily see if anything is over or under.
It will tell you precisely which staff have a noise risk in their job, and therefore who needs to have things like training, hearing protection or hearing testing. I can point you at known good providers for the hearing testing if that helps.
It will assess current and possible alternatives for hearing protection and confirm what is suitable for your specific noise risk - something the HSE often look to see in place.
It will also make suggestions for ways to reduce noise levels if possible.
And it will tell you when to repeat it.
A noise risk assessment
The duty on employers is to have a noise risk assessment, this is not complicated but only you as the client can complete it. It really is simple though - most of it is in my report, plus things like your PPE records or hearing testing programme. See the Managing Noise Safety pages for more information on the noise risk assessment.
“Thank you for all the noise safety information provided in the noise assessment and arranging it for us. Would just like to say I really appreciate all the knowledge you have shared with me as the guidance alongside the results really helped. This is a pretty new process for our site due to the recent introduction of new machinery and I have found the noise side of it very interesting. I will be sure to highly recommend your company to our sister site in England”. - H&S Manager, Irvine, Scotland
Noise assessments can even sometimes save you money
With a fair wind behind you and some luck, as well as keeping the HSE and your insurer happy, just occasionally a noise assessment can save a considerable chunk of money for clients. Recent cases have included:
A noise assessment for a new client who was also planning on getting over 200 hearing tests done every year as it sounded noisy in their factory. The noise assessment showed the averages to be well below the 85 dB(A) limit so hearing tests were not needed, a saving of around £4,600 per year.
A client had walked around their factory with a phone app looking at the noise, decided it was high, and several years ago started getting all 380 staff covered with hearing testing at a cost of about £8,700 a year. They asked for a proper noise assessment and it confirmed that of the 380 staff, they actually only needed to get hearing tests done for 14 of them. So from £8,700 to about £500, each year.
A small client had done hearing for years as they thought it was noisy, but the noise assessment confirmed it was not needed so that ongoing cost could be dropped as there was no risk.
Another small company had been told by their insurer that they thought hearing tests should be done as ‘it sounds noisy’. My noise assessment showed it was nowhere near the limits and was not needed, again, not just a one-off cash saving but every year as well.
Noise assessment and noise safety Q&A
Some of the common questions people have about noise safety at work. Also see the Managing Noise Safety pages for more in-depth help and information.
-
If an employer thinks levels may be close to 80 dB(A) then they have to get a noise assessment - they have to measure the noise levels.
That can be based on manufacturer’s data or things like a need to shout to be heard.
IF LEVELS ARE 80 TO 84 dB(A) OR 135 dB(C)
Do a noise assessment.
Employee noise safety training has to be given.
Hearing protection has to be made available.
The use of the hearing protection is optional for employees - they can choose whether to use it or not.
IF LEVELS ARE 85 dB(A) or 137 dB(C) OR OVER
Reduce the noise levels by engineering controls where reasonably possible.
Use organisational controls if possible, eg limiting exposure time by job rotation.
Hearing protection use is mandatory.
Hearing testing (audiometry) is mandatory.
-
I probably do at least one noise assessment each week where some unlucky soul opened their front door to find one or two horned devils from the HSE standing there. The Inspector had a steely glare behind the monocle over their one good eye and told the employer to sort out a noise assessment pronto.
My noise assessment reports will help you, covering the noise assessment needed for the Noise Regs., and helping stop the small business owner getting locked up in a cell for 23 hours a day with Big Dave the Troubled and Touchy Sex Pest.
One tip, if you have been told to review the need for the full gamut of noise assessment, hearing protection assessment and hearing testing (health surveillance), do the noise assessment first before booking things like hearing testing or buying more PPE in. The noise assessment will tell you if hearing testing is needed and if so who needs to be covered by it, and will specify what type of hearing protection to get - don’t forget ‘strongest is best’ is not the case for ear plugs or ear muffs so don’t buy hearing protection without a noise assessment in place first.
-
When I get there all I need is someone to show me around so I know what you want measuring and get an idea of the place.
After that I am pretty much self-contained and will crack on with the noise assessment, pootling along until I have all the measurements I need. I usually use multiple noise meters at once, depending on the specific jobs I am measuring.
How long does it take?
As long as is needed is the unhelpful answer really. I will be onsite for as long as I need to get all the data to be able to give an accurate assessment of the noise risks.
Because I can use up to 15 noise meters at once I can gather data very quickly. In the old days a noise assessor would maybe use one or two meters at a time whereas the investment I have made in noise meters means what used to be one meter used for 15 hours can now be 15 meters used for an hour and gather the same amount of data.
What is critical is the job cycle on the site - if the production cycle changes over several hours then that is how long I will be there to cover it all.
-
Certifications
I am certified in workplace noise assessment by the Institute of Acoustics.
As well as that, I have the NEBOSH Diploma ensuring I have a good overall understanding of health and safety principles and how noise slots into that.
I am also a member of the British Society of Audiology and certified in undertaking workplace hearing tests.
From the Institute of Acoustics I know how to assess noise risks. From the NEBOSH Diploma I know how noise assessment fits into safety at work. From the British Society of Audiology I know the health side of it and what noise does to hearing.
Experience of noise assessments
With 30 years of experience of industrial noise surveys in everything from joinery workshops to food factories, emergency services to ships, automotive industries to ship building, and companies from 5 to 2000 employees, I have experience of delivering high quality noise assessments in all workplaces.
Experience of health and safety
As well as the noise side of things, I have spent many years in the past bothering people about health and safety as well, before specialising in noise.
Having had the frankly ludicrous job title of 'Global Director, Health And Safety' for an American company (based in the UK) and then running a health and safety consultancy of around ten people for many years, I have a good grounding of where noise safety slots into general safety, and importantly how to sensibly apply noise risk management to a wide range of industries.
Why no CMIOSH or OSHCR?
I am not on the OSHCR for the simple reason that I am not a Health and Safety Consultant. Health and Safety Consultants do asbestos, lone working, electrics, working at heights, accident investigation, workplace safety, and on and on, whereas I just do noise assessment.
Back when I did all things health and safety I was CMIOSH for years, but when the decision was taken to focus purely on noise the rest of the CMIOSH stuff became irrelevant, so it was cancelled.
Often a specialist is best. Got an asbestos issue? Ask an asbestos consultant. Got a fire safety issue? Ask a fire safety company. Got a noise issue? Ask a noise specialist.
-
Noise levels
I measure the noise levels and give comparison to the Noise Regs limits.For noise nerds - I measure dB(A), dB(C) peaks, and give eight-hour daily averages (or longer if alternative shifts are used). I will use hand-held and wearable noise meters - whichever is most appropriate for the job.
Hearing protection assessment
I will assess the current hearing protection against the noise levels present to confirm all is OK. I will also give alternatives and tell you what SNR to aim for so you can choose others as needed in the future.Advice on other actions needed for the Noise Regs
As well as identifying the noise exposure levels and looking at your hearing protection, I will also make clear what other actions are needed. For example:Who needs training to be compliant with the Noise Regs, and what that training should cover.
Who should be included in a health surveillance (hearing testing) programme.
Advice on some possible physical noise-reduction measures.
Advice on other means of controlling exposures such as whether limiting exposures via using job rotation to reduce exposure time is possible or useful.
Where needs to be signed as mandatory hearing protection.
Other info
I change each report slightly to match the particular workplace and will make recommendations to match. My philosophy is that the report is changed to match your workplace, not that your workplace’s data is wedged into a standard report format.The noise assessment reports give a clear ‘this is the result, this is what it means and this is what other actions you may need to take’, avoiding the jargon which makes noise-nerds feel special but which doesn’t really help the client.
By the way, if you have Agency staff the report will cover this as well as the requirements for the employer can be a little different here.
-
This is covered in the noise assessment for you.
One of the biggest mistakes a lot of employers make, entirely via the best of intentions, is to get the strongest hearing protection they find, but stronger is not synonymous with ‘better’ and you can have too much as well as too little.
My noise assessment will cover the hearing protection issue for you, looking at:
Assessing the current hearing protection’s performance to make sure it is right for the noise risk.
Giving a list of suitable alternatives so you can choose others if you wish to change in the future.
Identifying who needs to use hearing protection at work.
Identifying who needs training about it.
Setting out what other ongoing measures the employer may need to have in place, such as monitoring and supervision of its use.
All that will cover the hearing protection issues for you.
-
The Noise Regulations, the actual law bit, simply say: ‘The risk assessment shall be reviewed regularly, and forthwith, if there is reason to suspect that the risk assessment is no longer valid; or there has been a significant change in the work to which the assessment relates’. That’s it for the actual law - review it when you think you need to.
The basic principle is that you should review the noise assessment when you have reason to believe things may have changed and possibly altered peoples' exposures to noise. For example, changes to a factory layout, introduction of new machinery, changes in how long machines are used, changes in shifts, etc.
A review can be a systematic check of the existing assessment looking to make sure nothing has changed; the machines are the same, the people the same, the shifts the same, etc. and if all is good, document that this review has been done and that's it, all sorted.
Even if you had the noise assessment itself done by an external consultant you can still do this review in-house - it is your business and you know if something has changed.
If nothing has changed, document that the review was done so you can prove when it took place, who was involved and what was looked at, and then you are done. This needn’t be too onerous and notes or minutes will suffice.
Do an in-house review at least annually and keep the record alongside the noise assessment.
As a recommendation for re-doing / repeating a noise assessment, for sites with a general noise risk I would recommend you re-do the assessment from scratch every three years or so. This is purely because although it may look like nothing has changed, some things inevitably will. Cutting heads may be increasingly worn and worn heads make more noise than sharp ones. Bearings may be wearing in a motor. A loose panel bolt can make a dramatic change in the noise levels. None of these will be apparent on a quick check so a policy of doing it again from scratch will act as a good fail-safe for you.
If your noise risks are particularly high or there are often changes to working practices or equipment, consider re-doing it from scratch every two years, but make that decision based on your assessment of your risks and whether you consider the noise risks to be high or not.
-
Technically there is a difference and what you need is a noise assessment.
A noise assessment is measuring the noise risk your people are actually exposed to. A noise survey can just be a plan of the site with some noise levels written on but that is not what the Noise Regs want. The Regs don't really care what noise a machine makes, they care what noise is received by people - an assessment of their personal noise risk.
But, 'noise assessment' and 'noise survey' are terms which are often used interchangeably so go with whatever you like. I do use both here as well as that is what people tend to use, but for clarity my noise assessment is the former - what noise people are exposed to, so in-line with what is needed by the Noise Regs.
-
Similar terminology but there is a slight difference between the two. The Managing Noise Safety section has more detailed information but effectively:
The noise assessment is the measuring of the noise levels and noise risk, assessing suitability of PPE, identifying who needs to wear PPE, who needs training and/or hearing testing, and making some noise exposure control suggestions.
A noise risk assessment is that, plus your PPE records, training records and health surveillance records. Usually the noise risk assessment is a dead simple document just referencing where everything else is. Only a client can complete that but it is a five minute job at most - most of the work is in the initial noise assessment.
-
A noise risk assessment can be very simple and is often a short document linking together various other documents and information sources within the organisation.
An example noise assessment template can be downloaded here.
-
To be honest, no, not all that useful.
The best way to explain that is a site I went to recently. They had an area where average noise levels were OK, about 77 to 78 dB(A), but had very brief periods where the noise jumped to about 88 dB(A) for a few seconds.
With the best of intentions they’d put one of those illuminating signs up and had a policy that when it lit up, hearing protection was needed. The problem was the sign flashed on occasionally and briefly, so everyone just ignored it.
The main issue though is that the Noise Regs are interested in the average noise level for a day, not really the peak dB(A), and an occasional peak of 88 dB(A) in an otherwise quiet area was pretty much irrelevant and had no material impact on people’s daily exposures, which remained well below the limit.
Noise signs where the noise is intermittent like this are therefore pretty useless in reality. If they only light up briefly then everyone ignores them, and they indicate hearing protection as needed when in reality it isn’t.
Illuminating noise signs don’t really add much even if the noise is high for a prolonged period, as then hearing protection is then mandatory and should be being worn anyway.
-
Yes. The limit of 85 dB(A) means that above this other requirements then apply, but it doesn't mean the job cannot be done.
“Thank you for all the noise safety information provided in the noise assessment and arranging it for us. Would just like to say I really appreciate all the knowledge you have shared with me as the guidance alongside the results really helped. This is a pretty new process for our site due to the recent introduction of new machinery and I have found the noise side of it very interesting. I will be sure to highly recommend your company to our sister site in England”. - H&S Manager, Irvine, Scotland